
Scheduled Maintenance
Optimal performance,
safety ensured.
We recognise the pivotal role that well-maintained lifting equipment plays in the success of your projects. Our dedicated scheduled maintenance service is designed to ensure not just the optimal performance but also the safety of your lifting equipment. Our commitment is backed by a meticulous schedule, featuring periodic inspections, designed to proactively address any potential issues and keep your lifting equipment in peak condition.
Explore our services: A showcase of Lincer’s work


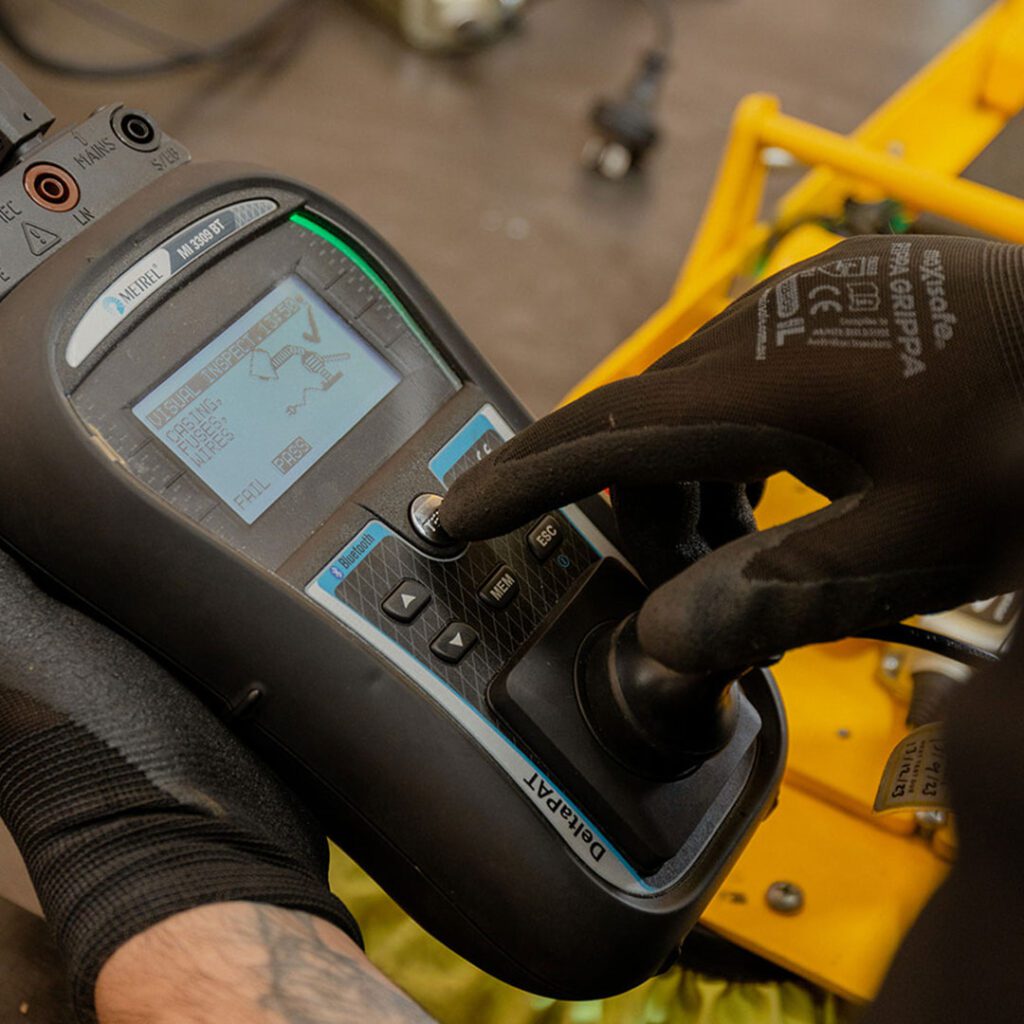
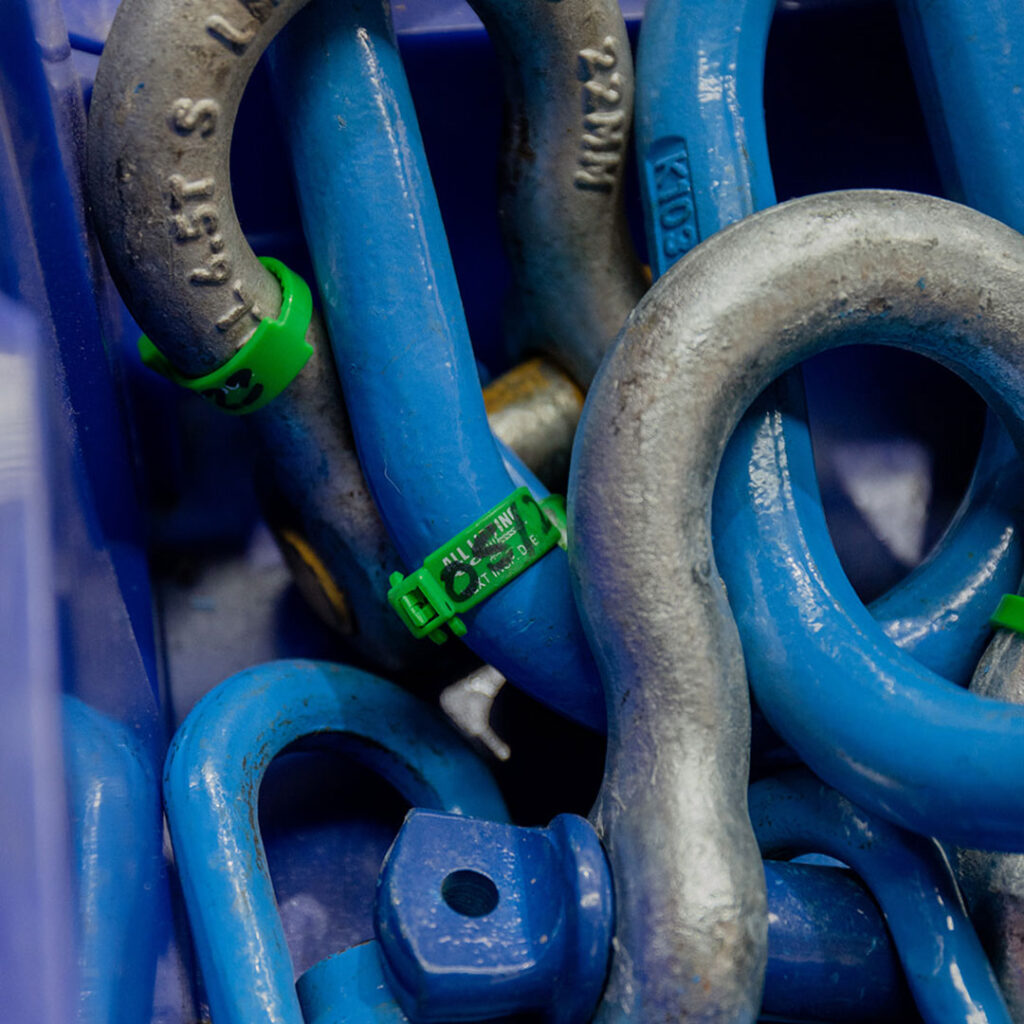
Enquiry form for Scheduled Maintenance for Lifting Equipment
Kindly fill out the form below to request our Scheduled Maintenance service, and our team will contact you shortly.
Australian Standards and Manufacturer Recommendations
In Australia, specific standards and regulations have been established to guarantee the effectiveness and safety of vacuum lifting equipment, and material handling equipment. These standards offer precise guidelines for performing inspections and upholding the functionality of lifting equipment.
At Lincer, we ensure the implementation of all manufacturer recommendations. We recognise that each type of equipment possesses distinct characteristics and may require different testing procedures. Our commitment lies in understanding and adhering to these unique specifications, ensuring the highest level of safety and efficiency for your equipment.
How We Schedule Equipment Maintenance at Lincer
Our proactive approach involves regular, thorough inspections of your lifting equipments every quarter. This scheduled maintenance allows us to identify and address any emerging issues promptly, preventing unexpected breakdowns and ensuring the reliability of your equipment.
Equipment
Conditions
Documents
Markings
Equipment
configuration
Equipment
Functionality
Testing
Schedule Maintenance Frequency
Scheduled maintenance is conducted concurrently with daily and pre-operational checks, as well as annual inspection and testing, based on specific equipment requirements. For details, refer to our Inspection and testing service
Equipment | Frecuency |
---|---|
Mini Floor Crane | Annual |
Glass Vacuum Lifter | Annual |
Glass Vacuum Robot | Annual |
Glass Vacuum Manipulator | Annual |
Walkie Reach Stacker | Quarterly & Annual |
Wire Rope Hoist Electric | Annual |
Forklift | Quarterly & Annual |
Scissor Lift | Quarterly & Annual |
Please note that the information provided may vary depending on different brand requirements. Additionally, references to local standards are subject to potential changes. For the most current guidelines, please consult with the supplier directly.
Why Choose Lincer for Your Maintenance Needs?
1.
Reliability:
Our certified technicians bring unmatched expertise to every maintenance task, ensuring precise analysis and effective solutions.
2.
Customer Satisfaction:
Our customer-centric approach means we’re here to support you at every step, providing transparent and efficient services.
3.
Technical Expertise:
Benefit from our in-depth technical knowledge, allowing us to address maintenance challenges with precision and efficiency.
Ensure the Longevity and Performance of Your Lifting Equipment.
Choose Lincer for your lifting equipment maintenance needs, and experience the peace of mind that comes with a proactive and reliable maintenance schedule. Our commitment to excellence, combined with periodic inspections and major testing at the end of the year, ensures that your equipment operates seamlessly, contributing to the success of your construction projects. Contact us today to schedule your equipment maintenance and elevate the efficiency and safety of your lifting equipment.
Get a visual guide from Lincer with essential insights on maintaining your Glass Vacuum Robot.
Don’t let equipment maintenance challenges hold you back. Empower your team with the knowledge they need to keep operations running smoothly.
Our Services
Lincer ensures your lifting equipment’s peak performance with thorough inspections, maintenance, repairs, and readily available parts. Discover our comprehensive suite of services below.
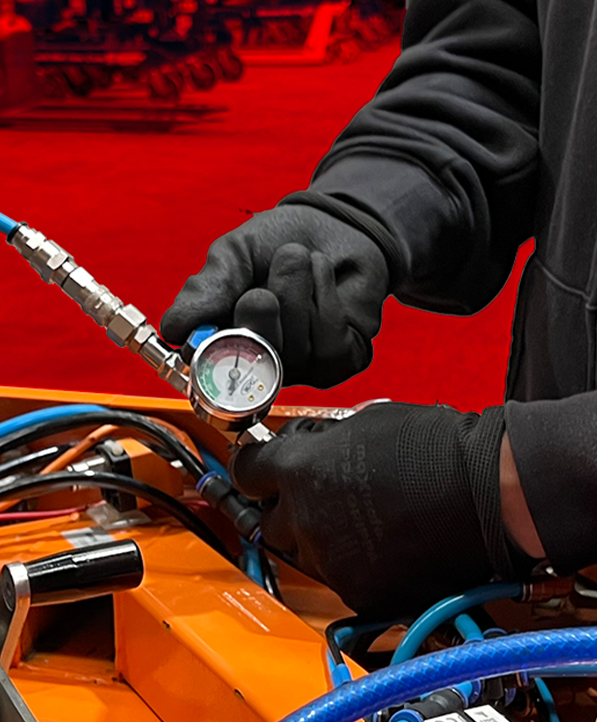
Inspection and Testing
Our comprehensive Inspection and Testing services vacuum lifting equipment, and material handling equipment are designed to safeguard your operations and workforce.
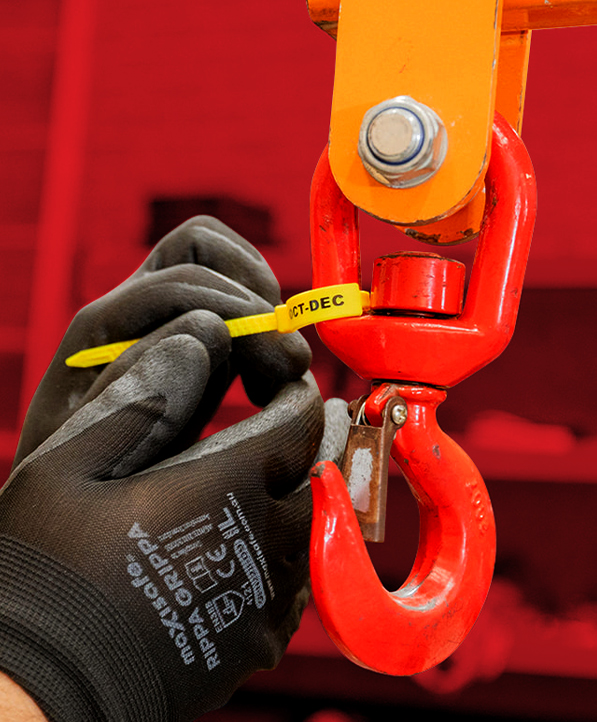
Schedule Maintenance
Our commitment is backed by a meticulous schedule, featuring periodic inspections, designed to proactively address any potential issues and keep your lifting equipment in peak condition.

Replacement Equipment
We offer replacement lifting equipment while yours is being serviced, ensuring your operations continue uninterrupted, keeping your projects on track.
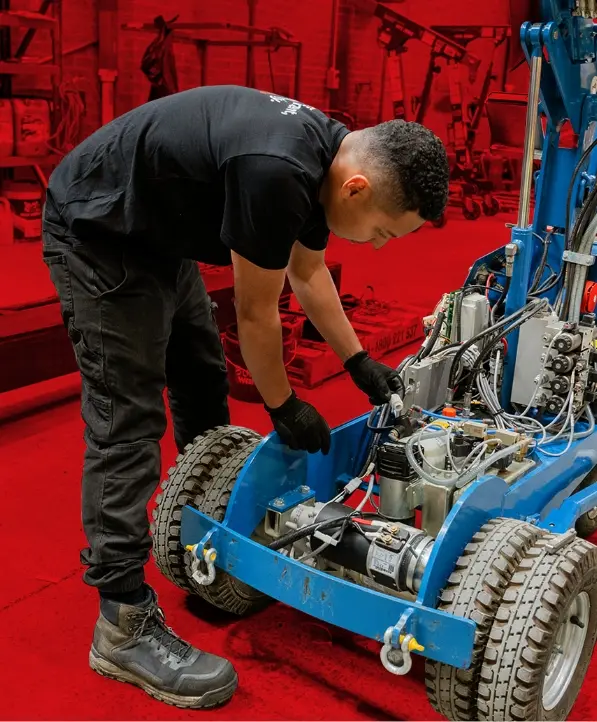
Repairs
At Lincer, we specialise in top-tier repair services for lifting equipment. Our certified technicians are adept at addressing any damage, ensuring your equipment operates at its best.
Client Support
Access our client support page for tools to resolve issues and find technical information on lifting equipment effortlessly.
Frequently Asked Questions
Can scheduled maintenance be tailored to specific lifting equipment needs?
Yes, maintenance schedules are customised based on the type of equipment. It’s important to thoroughly check all items as per the manufacturer’s specifications and Australian standards.
How can I ensure compliance with maintenance schedules for lifting equipment?
At Lincer, we utilise maintenance management software to track schedules, set reminders for upcoming inspections, assign clear responsibilities, and maintain up-to-date documentation. Upon your request, we can notify you when the next service for your equipment is due.
Is there a difference between scheduled maintenance and repairs for lifting equipment?
Yes, scheduled maintenance is proactive and planned, aiming to prevent issues before they occur. On the other hand, repairs or unplanned maintenance address unexpected breakdowns or failures that require immediate attention to restore functionality.