
Inspection and Testing
Ensuring Safety and efficiency in Construction.
At Lincer, we understand that safety and efficiency are paramount in the construction industry. Our comprehensive Inspection and Testing services for vacuum lifting equipment, and material handling equipment are designed to safeguard your operations and workforce.
Conducting annual and major inspections helps identify and address potential issues before they escalate into major problems. This ensures that the equipment remains in optimal working condition, reducing the risk of accidents and promoting a safe working environment. Additionally, regular maintenance and testing can help extend the lifespan of the equipment, maximising its efficiency and productivity.
Some of the brands of lifting equipment we service



Enquiry form for Inspection and Testing
Kindly fill out the form below to request our Inspection and Testing service, and our team will contact you shortly.
Australian Standards and Manufacturer Recommendations
In Australia, specific standards and regulations have been established to guarantee the effectiveness and safety of vacuum lifting equipment, and material handling equipment. These australian standards offer precise guidelines for performing inspections and upholding the functionality of lifting equipment.
At Lincer, we ensure the implementation of all manufacturer recommendations. We recognise that each type of equipment possesses distinct characteristics and may require different testing procedures. Our commitment lies in understanding and adhering to these unique specifications, ensuring the highest level of safety and efficiency for your equipment.
How we inspect and test lifting equipment
Conducting a thorough lifting equipment inspection involves several key steps. These steps ensure that all critical components of the equipment are inspected and any potential issues are detected. The inspection process typically includes visual examinations, testing, and documentation requirements.
Equipment
Conditions
Documents
Markings
Equipment
configuration
Equipment
Functionality
Testing
Frequency of service Inspections and Testing
The frequency of inspections and testing varies depending on factors such as equipment type, usage, and adherence to Australian standards and manufacturer recommendations. Please refer to the table below for the recommended inspection and testing frequencies for vacuum lifting equipment and material handling equipment. Annual inspections are conducted concurrently with scheduled maintenance intervals based on specific equipment requirements. For details, refer to our Schedule Maintenance Service.
Equipment | Frecuency |
---|---|
Mini Floor Crane | Annual |
Glass Vacuum Lifter | Annual & Major |
Glass Vacuum Robot | Annual |
Glass Vacuum Manipulator | Annual |
Walkie Reach Stacker | Annual & Major |
Wire Rope Hoist Electric | Annual |
Forklift | Annual & Major |
Scissor Lift | Annual & Major |
Please note that the information provided may vary depending on different brand requirements. Additionally, references to local standards are subject to potential changes. For the most current guidelines, please consult with the supplier directly.
Benefits of Annual and Major Inspection and Testing
Lifting Equipment
1.
Expertise in Compliance:
Lincer brings extensive knowledge and expertise in adhering to industry standards, ensuring that your cranes, vacuum lifting equipment, and material handling equipment comply with regulations. This expertise is vital for maintaining a safe working environment.
2.
Proactive Issue Identification:
Our annual and major inspections go beyond routine checks. Lincer employs a proactive approach to identify and resolve potential issues before they escalate.
It’s important to understand that owners and operators of equipment bear the responsibility for ensuring that their equipment is up to date with service and safe for use prior to each operation through pre-start checks.
3.
Efficiency Optimisation:
Optimal maintenance provided by Lincer correlates with improved operational efficiency. Well-maintained machinery operates reliably, reducing the occurrence of breakdowns and associated downtimes. This translates into increased productivity and cost-effectiveness for your business.
4.
Tailored Solutions:
Recognising that each piece of equipment has unique characteristics, Lincer provides tailored solutions. Our services are customised to meet the specific needs of your machinery, ensuring optimal performance and safety.
5.
Prolonged Equipment Lifespan:
Lincer’s routine inspections and testing facilitate the early detection and rectification of minor issues. This proactive approach significantly prolongs the lifespan of your lifting equipment, reducing the need for costly replacements. By choosing Lincer, you maximise your return on investment and ensure the prolonged functionality of your equipment.
Your equipment, Our priority. Partnering with Lincer means servicing machines while investing in longevity, safety, and efficiency.
Get a visual guide from Lincer with essential insights on maintaining your Glass Vacuum Robot.
Don’t let equipment maintenance challenges hold you back. Empower your team with the knowledge they need to keep operations running smoothly.
Our Services
Lincer ensures your lifting equipment’s peak performance with thorough inspections, maintenance, repairs, and readily available parts. Discover our comprehensive suite of services below.

Inspection and Testing
Our comprehensive Inspection and Testing services vacuum lifting equipment, and material handling equipment are designed to safeguard your operations and workforce.
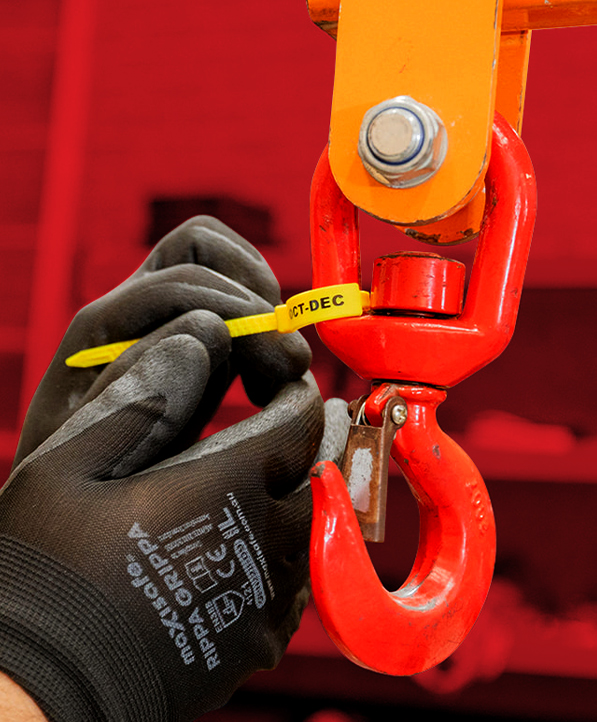
Schedule Maintenance
Our commitment is backed by a meticulous schedule, featuring periodic inspections, designed to proactively address any potential issues and keep your lifting equipment in peak condition.

Replacement Equipment
We offer replacement lifting equipment while yours is being serviced, ensuring your operations continue uninterrupted, keeping your projects on track.
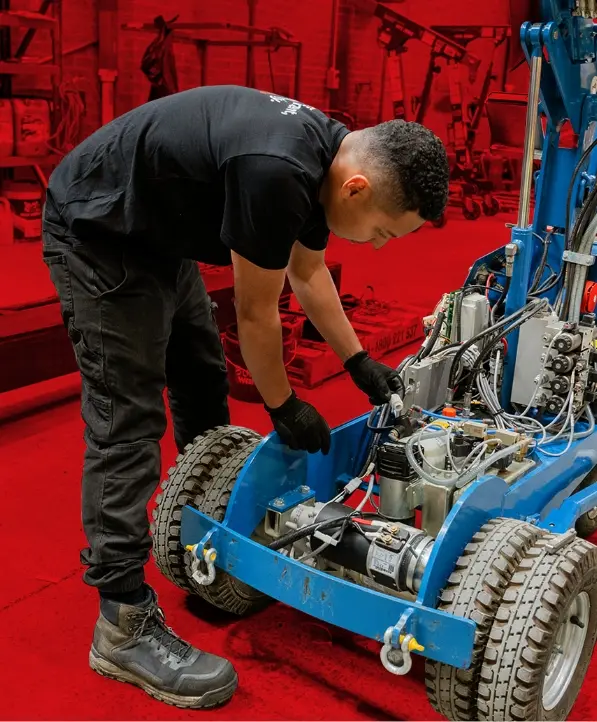
Repairs
At Lincer, we specialise in top-tier repair services for lifting equipment. Our certified technicians are adept at addressing any damage, ensuring your equipment operates at its best.
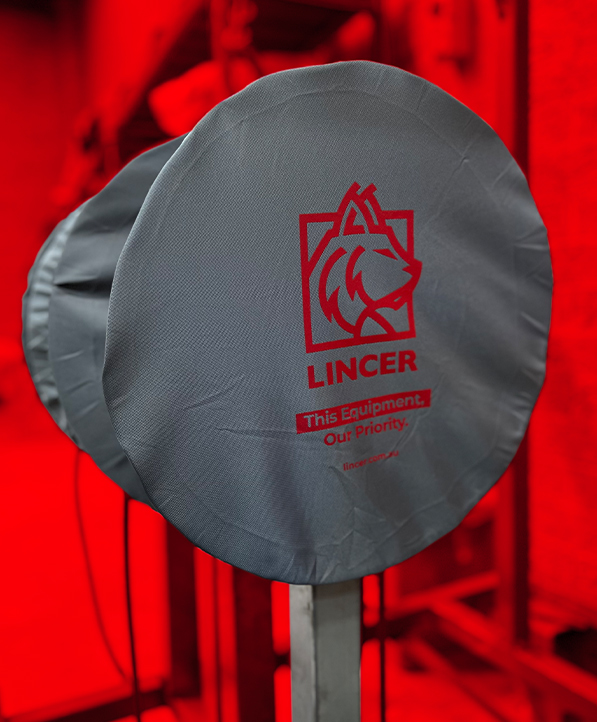
Parts
Discover high-quality lifting equipment parts at Lincer. We offer a wide range of genuine parts to keep your equipment at peak performance.
Client Support
Access our client support page for tools to resolve issues and find technical information on lifting equipment effortlessly.
Frequently Asked Questions
How often should lifting equipment be inspected?
The frequency of inspections depends on factors such as the type of equipment, its usage, and the environment. Typically, thorough examinations are required at regular intervals, ranging from daily visual checks to detailed annual inspections.
Please contact us to find out when the next inspection for your equipment is scheduled.
What is involved in a lifting equipment inspection?
Inspections involve a range of checks including visual inspections for signs of wear or damage, functional tests to ensure proper operation, examination of load-bearing components, and verification of compliance with safety regulations and standards.
What are the consequences of not inspecting lifting equipment?
Failure to inspect lifting equipment can lead to safety hazards, potential accidents, equipment failures, legal liabilities, and operational downtime.
Can lifting equipment inspections be outsourced to third-party providers?
Yes, many organisations opt to outsource inspections to specialised third-party providers equipped with the necessary expertise and equipment to conduct thorough examinations and issue compliance certificates. At Lincer, we provide equipment servicing and serve as your dedicated asset manager to prevent interruptions.